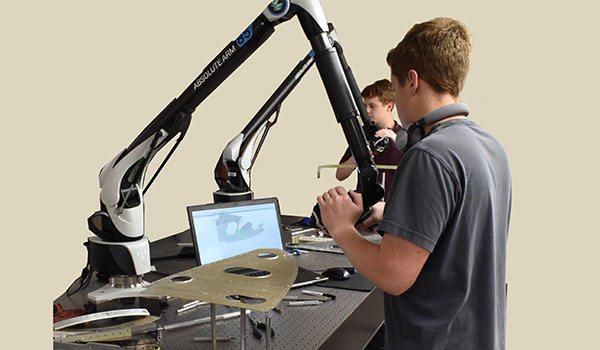
AMCOM Command Sergeant Major / By CSM Mike Dove: In the fall of 2019, the U.S. Army Aviation and Missile Command (AMCOM) in conjunction with the Program Executive Office Aviation, the Future Vertical Lift Cross-Functional Team and the Systems Readiness Directorate of the Combat Capabilities Development Command Aviation and Missile Center teamed together to commission a study on the operational availability and materiel availability for future vertical lift systems with Wichita State University (WSU).
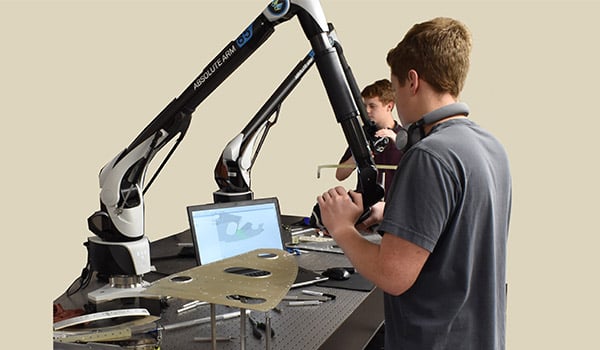
National Institute for Aviation Research personnel use high fidelity scanners during the reverse engineering of the UH-60L./ NATIONAL INSTITUTE FOR AVIATION RESEARCH, WICHITA STATE UNIVERSITY
A few months into the study in January 2020, AMCOM leadership and primary sustainment representatives from each organization were invited to attend a briefing by WSU leadership on their capabilities, an update on the study and how other military services were utilizing WSU to create a digital twin of their aging fleet of aircraft. At the time of the visit, each of the other services had already completed or started a digital twin effort with WSU. In conjunction with the Secretary of Defense Strategic Capabilities Office, the Army is able to begin the process of creating a digital twin utilizing two UH-60L Black Hawks which were delivered to WSU in May 2020.
Origins of the Digital Twin
What exactly is a digital twin and how can it be used? According to the National Aeronautical and Space Administration (NASA), “A Digital Twin is an integrated multiphysics, multiscale simulation of a vehicle or system that uses the best available physical models, sensor updates, fleet history, etc., to mirror the life of its corresponding flying twin.” NASA created the idea of a “twin” during the Apollo 13 mission when the world heard the famous phrase “Houston, we have a problem.” NASA was forced to create a mock-up of the space capsule on the ground to solve the problem the astronauts were experiencing in space. NASA even created the Space Shuttle Pathfinder as a full scale replica of the Space Shuttle Enterprise known as a Facilities Test Article to test equipment, cranes, lifting devices and transport equipment in order to prevent damage to the actual orbiter. The Pathfinder is on display in Huntsville, AL at the Space and Rocket Center. All this leading to NASA being the first to introduce the term “digital twin” in 2010 in their Technology and Roadmap for 2011 and 2012.
Army’s Digital Twin
Fast forward to the digital age of the 21st century, the Internet of Things, and the Industrial 4.0 revolution. Prior to computer aided drawings and now Global Finite Element Models (GFEM), aircraft drawings were two-dimensional blueprints, drawn to scale, on a flat piece of paper. Each measurement of every angle, thickness and type of material were included in these drawings. All of the Army’s enduring aircraft were created using two-dimensional, paper blueprints. That was the standard. One of the many digital standards used today is the GFEM which is quite impressive when viewed on the computer. The drawings are true three-dimensional representations of the parts and can be rotated on the computer so the engineer or vendor contracted to build a product can have a better understanding of the design of the part. WSU is actively creating the GFEM file for the UH-60L and AMCOM will have the first batch of digital files by the time this article is printed.
Sustainment Benefits
Sustainment of the enduring fleet provides challenges and opportunities. One of the challenges to sustain the Army’s enduring fleet is the ability to acquire or produce obsolete parts. In fact, there are more than 500 parts vendors will not submit a bid to produce because there is not a digital drawing for those parts. The Army will continue to fly the UH-60 Black Hawk, the AH-64 Apache, and the CH-47 Chinook for several more years, actually decades. Therefore, it is not only nice to have these digital drawings, it is imperative to provide logistical sustainment. Some of the benefits that can be achieved with digital drawings include the ability to manufacture more efficiently, additively manufacture parts, reduce repair times and improve recapitalization processes at the depot.
Training Benefits
Similarly to how NASA developed the need for a twin to tackle a complex problem, the digital twin can be used to train pilots and maintainers. In a sense, the flight simulators used by the Army are digital twins. Simulators digitally represent the aircraft and flying conditions where pilots train for multiple scenarios, multiple times to create muscle memory and confidence in their ability to operate very complex aircraft at significantly reduced costs and risk to human lives. What about the maintenance professional? At the last few Army Aviation Association of America and Association of the United States Army symposiums, original equipment manufacturers and third party vendors presented several versions of digital maintenance trainers as a method to train aviation mechanics. Some of these digital training devices and concepts are simple yet impressive and allow the mechanic to train the task prior to performing the task on the aircraft. The concept is not new to the Army. The 128th Aviation Training Brigade at Fort Eustis, VA actually has digital trainers for the avionics maintainers at the school to create scenarios for mechanics to troubleshoot electrical problems on the AH-64 Apache. The National Guard Western Army Aviation Training Site operates an LUH-72A maintainer course which includes a portion of the instruction using a digital maintenance trainer. The challenge now is getting this capability to the mechanic in the field and not just at the school.
The digital twin is the future of manufacturing, logistics, prognostics, training and several additional areas. The Army now requires Original Equipment Manufacturers of future vertical lift platforms to use digital twin technology. AMCOM, the Army aviation enterprise, and the users of these systems will all benefit from the implementation of digital twin technology. AMCOM and the Army aviation enterprise are making remarkable achievements, but more work is required in the areas of digital engineering, advanced and additive manufacturing and improving the supply chain. The future is upon the Army and modernization is happening now.
CSM G. Mike Dove is the command sergeant major of the Aviation and Missile Command at Redstone Arsenal, AL.