
AMRDEC Tech Talk / By Mr. Nathan Fulks: U.S. Army rotorcraft fuel cells qualified to MIL-DTL-27422 (Aircraft Ballistic-Tolerant Crash Resistant Fuel Tank) are designed for survivability in two ways. First, they are designed to retain fuel during a survivable crash in order to prevent post-crash fires.

Workers prepare an MH-47 fuel cell to be released as part of a fuel cell drop test. / AMRDEC AED COURTESY PHOTO
Secondly, they are designed to “self-seal” when penetrated by small arms fire. This column focuses on the crashworthy capability of these fuel cells.
Prior to the development of the crashworthy fuel system (CWFS), thermal injuries and fatalities were significant in helicopter crashes. During the Vietnam War there was concern over the increasing number of personnel killed or injured from post-crash fire burns received during otherwise survivable crashes. In the late 1960’s, the U.S. Army allocated resources to research and develop a CWFS for Army helicopters and, in 1970, the first Army helicopter equipped with a CWFS came off the production line. Table I shows accident data collected from 1967-1969, a time period when no CWFS’s were installed on Army helicopters, and from 1970-1976 when CWFS’s were being installed/retrofitted.
Correcting Inaccuracies
Initial versions of the crashworthy, ballistic tolerant fuel cell qualification specification for U.S. Army rotorcraft relied on the premise that the aircraft structure would protect the fuel cell during a crash and minimize puncture hazards. Research revealed that fuel cells are often torn away from aircraft structure, and need to be able to withstand crash loads independent of the surrounding structure. Another shortcoming was that the properties of the material used to construct the fuel cell were determined using arbitrary ultimate load factors without any crash impact testing to substantiate the design.
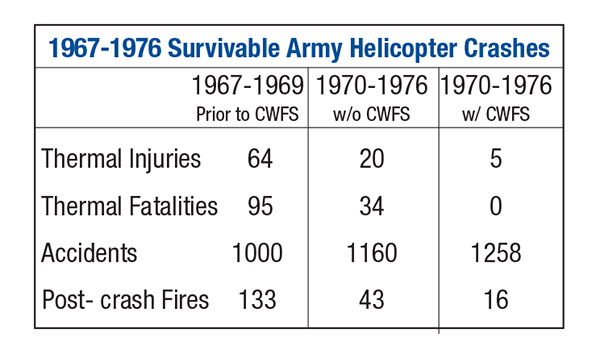
Subsequent work revealed that the acceleration environment during a crash can be considerably more than the arbitrary design load that was set forth in MIL-T-27422 and MIL-T-27422A. Research and testing showed that the requirements in MIL-T-27422A were inadequate and resulted in the development of qualification tests for penetration resistance, tear propagation resistance, and material strength as well as the 65 foot unsupported drop test. These changes were incorporated into MIL-T-27422B (Feb. 1970).
The Drop Test
The 65 foot drop crash impact test requirement was derived from analytical methods and empirical evidence gathered in testing, and was also verified by impact velocity data gathered from accident investigations. This data showed that the 95th percentile survivable accident corresponded to a 42 ft/sec velocity change in the vertical direction and a 50 ft/sec velocity change in the horizontal direction. This equates to a cumulative velocity change of 65 ft/sec. To achieve this velocity from a vertical drop, as done in the crash impact test, the fuel cell must be dropped from a minimum height of 65 feet. While 65 feet is the minimum vertical distance for the crash impact test, this leaves no margin of safety over a strict 95th percentile survivable crash. Starting with MIL-T-27442B, the fuel cell was required to be filled to 100% capacity with water. By filling the fuel cell to 100% capacity with water instead of the equivalent fuel weight, a margin of safety is achieved due to the fact that water is approximately 20% more dense than fuel.
Since the adoption of crashworthy fuel systems by the U.S. Army, dangerous fuel spillage in survivable helicopter crashes has essentially been eliminated, and thermal injuries and fatalities have been reduced to near zero. In fact, ground vehicles have started implementing similar designs. In his testimony before the House Armed Services Committee on May 8, 2013, Rep. Phil Gringey, M.D. of Georgia presented the case for putting in place measures to prevent post-event fires in U.S. military ground vehicles. He testified that, “Since 2003, according to U.S. Army reports, over 800 military burn casualties have occurred in support of Overseas Contingency Operations. The aviation community adopted standards and specifications (such as MIL-DTL-27422) to define survivability that have successfully prevented thermal injuries. I would ask the Committee to consider similar measures department wide through Thermal Injury Prevention Strategies (TIPS).”
Mr. Nathan Fulks is an engineer on the Hydraulic/Subsystem Team for the Aviation Engineering Directorate of the U.S. Army Aviation and Missile Research, Development, and Engineering Center located at Redstone Arsenal, AL.