
Arming the Force / By COL David Warnick, LTC Phillip Rottenborn, Mr. Forrest Collier, and Mr. Timothy Kay: As part of the Army Aviation and Missile Materiel Enterprise, the Joint Attack Munition Systems (JAMS) Project Office develops, fields, and sustains versatile weapon systems for the U.S. Army, Joint, and Coalition War-fighters, providing decisive advantages. For more than 30 years, the JAMS Project Office (under many names) has delivered more than 80,000 HELLFIRE missiles and 4.5 million Hydra-70 rockets/motors to the U.S. Warfighters and coalition partners. Today, the JAMS Project Office consists of three product offices: the Aviation Rockets and Small Guided Munition (ARSGM) Product Office responsible for Hydra 70 and Army requirements for the Advanced Precision Kill Weapon System (APKWS); the HELLFIRE Product Office whose responsibility includes all variants of the AGM-114 missile, and the Joint Air-to-Ground Missile (JAGM) Product Office. Each office has overcome unique production challenges in order to carry out the mission.
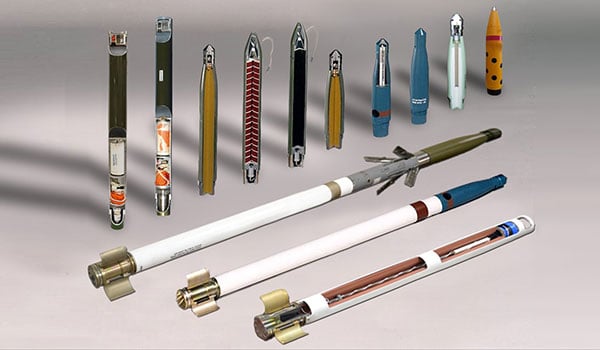
Hydra Family of Munitions / PM JAMS COURTESY PHOTO
Production Challenges
The HELLFIRE missile system was first produced in the early 1980s and is one of the most in-demand air-to-ground missile systems (AGMS) as it provides a critical capability for U.S. and foreign military sales (FMS) partners. As such, demand is at an unprecedented level and is driving an atypical production rate for such a complex AGMS. Successfully meeting this increased demand presents significant challenges, especially as the demand extended HELLFIRE production beyond the planned life of the program. Key challenges include supplier lead times, obsolescence management, facilitizing ramp-up to accommodate higher production rates, affordability, and adopting existing inventories to support the changing threat environment.
The extended production created supply chain management issues with availability and obsolescence management necessitating several major design and producibility upgrades while making the missile more affordable. Another challenge was facilitizing the HELLFIRE industrial base and increasing suppliers’ production rates while maintaining product quality. HELLFIRE production capacity increased 100 percent in the last five years with additional capacity increases planned. Managing production requirements, contracts, joint expenditures, and funding allocations for multiple services and FMS partners adds to the challenge of ramping up to higher production levels.
Unique Requirements
For unique requirements that were not appropriate for typical production, the HELLFIRE Product Office sought other options such as modifying the existing HELLFIRE and HELLFIRE Longbow missile inventory to create unique capabilities that quickly met changes in the operational threat environment. One such example was the modification of HELLFIRE Longbow missiles for engagement of littoral targets and to counter unmanned aerial vehicles. This flexibility enabled the HELLFIRE team to continue to meet the Warfighter’s requirements now and in the future while the next-generation JAGM missile completes development and is fielded.
JAGM
The Joint Air-to-Ground Missile (JAGM) will soon enter the inventory as a single missile replacement for both laser HELLFIRE and Longbow missiles after thousands of hours of design, testing, and issue identification and resolution. Throughout development, the program experienced numerous challenges, but managed to persevere and is poised to replace HELLFIRE as the most capable air-to-ground missile in the world. As the program proceeds through the Engineering and Manufacturing Development phase, it clearly has come a long way from engineering assets produced in laboratories to a design capable of full rate production (FRP).
JAGM’s primary technical task was the integration of both a laser and a radar sensor in the same guidance section. While both sensors were proven technologies, integrating and enabling each to leverage from the other proved challenging. It required a modernization effort to reduce size and an engineering effort to enable both to work in tandem. This effort required a highly complex transceiver that demanded extraordinarily tight component tolerances. These demanding requirements, coupled with a lack of institutional knowledge in transceiver development, led to low initial production yields and high re-work rates. A Yield Improvement Team was formed to proactively head off these challenges. This disciplined approach to attacking and overcoming issues enabled the program to continue to move transceiver production successfully down the learning curve.
The complex hardware requirements drove an equally in-depth software development effort. Additionally, JAGM’s requirement for interoperability on multiple aircraft required programmers to develop software enabling full missile functionality across all HELLFIRE capable platforms while applying unique capabilities never before fielded.
These features required significantly more advanced modelling and simulation (M&S) than required of legacy systems, with the Aviation and Missile Research, Development, and Engineering Center’s (AMRDEC) hardware-in-the-loop facility meeting that challenge. Combined with the Integrated Flight Simulation, the M&S capabilities mitigated costly redesign by detecting issues throughout the design process and enabling timely resolution in the development phase. Additionally, these facilities largely precluded the need for costly platform testing early in the program, as the design matured.
Despite a number of complex challenges, JAGM is producing test assets. The implementation of a disciplined yield improvement process coupled with leveraging world-class M&S systems has enabled the program to find and resolve issues early in order to deliver a game-changing air-to-ground capability to the Warfighter on time. Following the execution of a successful limited user test this year, JAGM will complete Low Rate Initial Production (LRIP) and proceed to FRP with a planned IOC of 4QFY18.
Hydra-70
The Hydra-70 family of munitions also provides close air support to ground forces and is designed for anti-materiel, antipersonnel, and enemy suppression missions. The Hydra-70 system has been in production for over 50 years with a relatively stable design. This legacy has presented its own challenges when attempting to modernize the baseline and incorporate new capabilities such as precision guidance.
Through more than a decade of sole-source production, many subcontract suppliers developed company-unique processes for building rocket components. A thorough update of the Government Technical Data Package required the incorporation of several hundred engineering changes for the design to be effectively competed. Some suppliers had difficulty transitioning from obsolete industry specifications and Hydra-70 unique detail specifications to the updated requirements. In the end, a baseline was established that will enable a competitive process to be followed while ensuring delivery of quality products.
In FY14, the Army revalidated a requirement to incorporate a precision guidance capability to the Hydra-70 rocket family through the integration of the Navy-managed APKWS semi-active laser guidance section. When mated with a 2.75-inch unguided rocket, this requirement greatly increases the accuracy of the rocket and complements the 30-millimeter cannon and HELLFIRE missile for AH-64 Apache platforms. This combination was successfully fielded by the U.S. Marine Corps on AH-1 and UH-1 helicopters for Operation Enduring Freedom; the Army validated an operational need for AH-64 to employ this capability in FY12. To support this new requirement, ARSGM worked with the Navy to procure APKWS guidance sections, as an element of the Hydra-70 program, in order to meet the operational need.
Throughout its history, the JAMS Project Office has managed the Army’s Aviation Weapons portfolio and sought to integrate new technologies and capabilities to provide a decisive advantage to Warfighters. Providing this advantage meant overcoming obstacles and production challenges. In a challenging fiscal environment, this Project Office continues to rise to the challenge of increasing production and addressing urgent requirements, all while developing the next generations of AGMS and precision munitions. As threats continue to evolve, JAMS will continue to anticipate and overcome the production challenges necessary to field Army Aviation platforms with the most lethal systems available in the world.
COL David Warnick is the project manager of Joint Attack Munition Systems; LTC Phillip Rottenborn is the product manager for Joint Air-to-Ground Missile; Mr. Forrest Collier is the product manager for HELLFIRE; and Mr. Timothy Kay is the product lead for Aviation Rockets and Small Guided Munitions – all are located at Redstone Arsenal, AL.