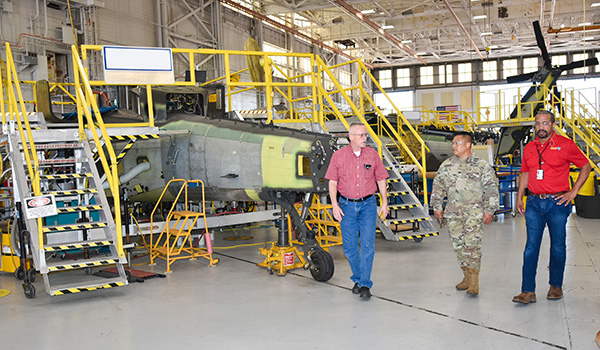
By COL Allan H. Lanceta and Brigitte Rox: The Corpus Christi Army Depot is the Army’s organic industrial base for helicopter maintenance, repair and overhaul. We have been a driving force in defense as the Army’s premier in-house capability to sustain Army and similar defense rotary wing aircraft assets.
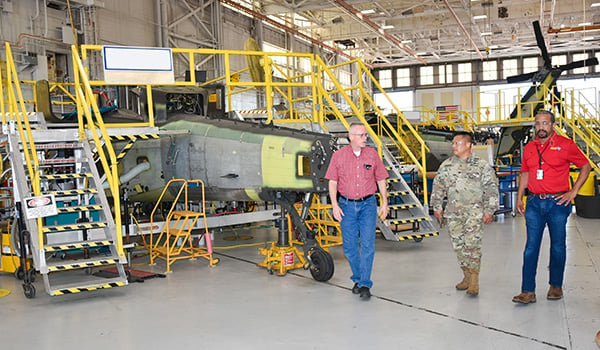
U.S. ARMY PHOTO BY BRIGITTE ROX
CCAD’s recapitalization, or recap, program is vital to the Army’s modernization effort as it updates and extends the life of existing UH-60 Black Hawks in the Army inventory.
The Army has turned to us as their trusted solution of helicopter sustainment for 56 years. The depot is currently recapitalizing L-model Black Hawks, but that work will be replaced by the UH-60V upgrade in Fiscal Year 2018.
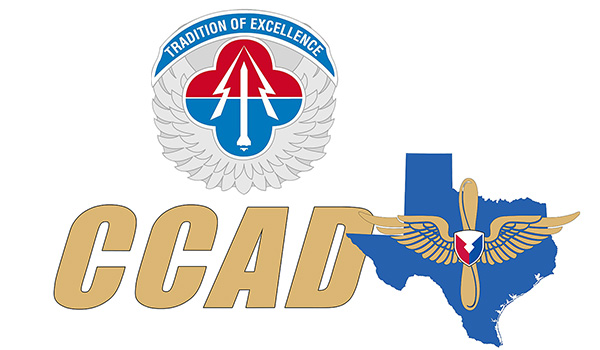
The UH-60V recap program is one of the Army’s “shovel ready” programs delivering readiness as intended through the Army Modernization Strategy. It offers an incremental upgrade nearly identical to the advanced UH-60M capabilities at a lower cost to the taxpayer, extending the life cycle and enabling the technologically advanced aircraft to reach the Soldiers faster so they can fight and win in the next mission.
The Art of the Probable
Operating as an Army Working Capital Fund, CCAD’s products and services must match the best in the industry, sustaining readiness on schedule and at a competitive price. CCAD has been working on a number of initiatives to increase aviation sustainment’s efficiency. Automation through the Logistics Modernization Program makes our depot more transparent as we acquired the ability to trace every part for every aircraft across the enterprise. To leverage this tool effectively, we initiated a new business model that focuses on eliminating constraints at its source to create a well-oiled machine of efficiency. This model, which we now call the Art of the Probable (AoP) at CCAD, is already resolving constraints that have existed here since the dawn of depot-level maintenance, repair and overhaul (MRO).
Reshaping Materiel Readiness for the Victor
Equipping our Soldiers with mission-ready helicopters is one of the Army’s top priorities which is why MG Douglas M. Gabram, commanding general of U.S. Army Aviation and Missile Command challenged us to upgrade our UH-60s faster than we ever have before – 275 days.
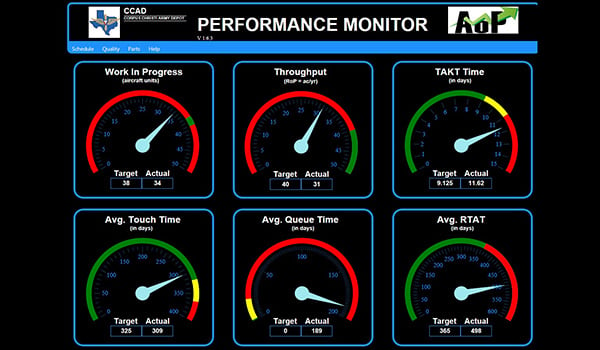
CCAD tracks its UH-60 program using AoP Dashboards that continually monitor performance. The Schedule Control Center measures performance through a specific schedule-related interface consisting of six gauges.
On October 3, 2016 CCAD took its first critical steps to deliver synchronized materiel readiness by incorporating the AoP business model into the UH-60 recap line. Armed with our new goal and business model, our depot leaders and other top talent became our AoP core team responsible for trestructuring our most robust production line: a UH-60 recapitalization line that had been in place since we upgraded our first A-model.
The core team started by assigning a gate number to capture every major step of our recap process. Each gate’s corresponding director or appointed core member serves as that gate’s process owner, responsible for executing change as required.
The Power of Gate Zero
Sustainable materiel readiness requires teamwork, communication and visibility throughout the entire enterprise from the very beginning of the process – way before CCAD receives a helicopter for work. Before accepting any work or seeing any aircraft, there’s logistics. We call this pre-induction, or planning, work Gate Zero. This is the nervous system through which the UH-60 recap program could move.
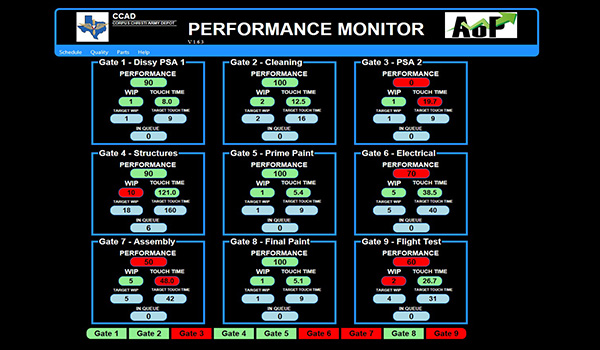
Gate level monitors track the performance of individual gates within each machine. The monitor shows target and actual values for works in progress, capacity and touch time of each gate.
Materiel flow has been a consistent inhibitor with our aircraft, but we never realized the extent of the issue until our supply chain tracking system was automated through our Logistics Modernization Program (LMP). When we drilled down to tackle this constraint, we realized the only solution was to forecast each helicopter’s required work and materiel needs early and more accurately. Now we are reexamining our processes and supply chain to pinpoint and eliminate constraints that have gone unaddressed for years.
Our team of logisticians is currently working behind the scenes syncing our capabilities and capacity to meet our customers’ aviation needs. This improves our ability to accurately forecast our delivery date to the customer. This, in turn, shows customers that CCAD schedules to promise, and that we are reliable and ready to meet their supply needs.
Not only that, but we have improved our communication and relationships within the depot organization, with our suppliers at the Defense Logistics Agency and at the AMCOM Logistics Center. We are bringing materiel readiness to the 21st century and it’s only going to get better.
Process was another inhibitor. Our process for requesting parts was not effective because we were not talking to each other or using our logistics system to its fullest potential.
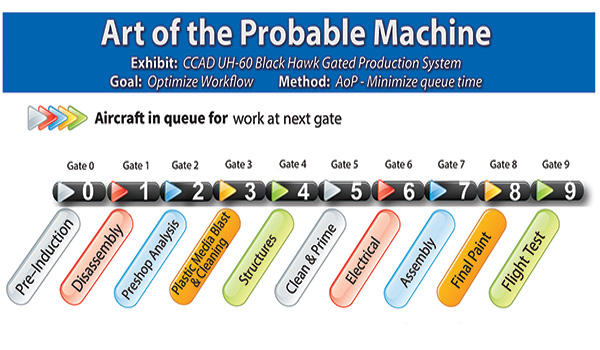
By utilizing LMP and understanding that CCAD has enough historical data to predict or forecast 80% of the parts we have consumed in the past, we could begin to attack it with solutions, continually evolving Gate Zero until we went from being 27% parts supported to being 97% parts supported on average. Now CCAD teams look as far out as 120 days to begin forecasting to ensure materiel meets the aircraft at the point of need.
This is the power of Gate Zero. It would not have been possible without fully adopting the new automation software, AoP or without the great support we’re getting from DLA and AMCOM.
Logistics Center
Gate Zero became a game changer for the UH-60 recap line. We now access more data on incoming aircraft before it arrives to our shops; every second of aircraft maintenance is on record. Be it inspections or modifications, every pilot has recorded all the information and it’s all digitized so we know what we’re working with and the customer knows what they are getting and when they are getting it. We don’t want to take flying aircraft out of operation just to sit in a hangar; when aircraft are here, each day counts.
At any time, anyone at the depot can check the status of our UH-60 aircraft through our AoP Dashboard to gauge the work flow in every gate. The dashboard tells you how many aircraft are in queue at each gate, the average queue time, average days aircraft spend being serviced at each gate – everything. You can dive down even deeper to track each aircraft by tail number, including the incoming H-60s. The dashboard gives users full transparency.
A key element of AoP is centered on constraints, or opportunities for improvement. The idea behind the Theory of Constraints is that, once you eliminate one constraint, you target and eliminate the next one and you keep going, making your machine better and better, improving the work flow, reducing the amount of queue time helicopters wait before they can move to the next gate.
Once there are no helicopters in queue at one gate, you eliminate the queue at the next gate until no queues exist anywhere in the process. Then inventory can be reduced for efficiency. That is why a strong and reliable supply chain is necessary. This level of accuracy improves our ability to perform to promise for our customers, and it adds confidence to our artisans, our product, speed and quality.
Supercells
To effectively monitor and ensure cross-communication amongst our directorates, we implemented a ‘supercell’ concept within each production program. Supercells are loosely taken from a Joint Operations Center methodology wherein all military operations are temporarily working together, holistically, to defeat a common threat.
We have incorporated that holistic view into our Supercell concept to improve sustainable materiel readiness in depot-level helicopter maintenance. Our supercells are divided into programs, like the UH-60 Recap Supercell, the T-500 Engine Supercell, the AH-64 and CH-47 Supercells. Each cell consists of the program managers, aircraft production, supply chain, production control and local manufacturing personnel tied to that product or program.
Their job is to identify and access each individual aircraft for materiel and production supportability. Supercells eliminate communication and visibility barriers existing between departments so they can effectively focus on the job at hand as an enterprise.
Every process at the depot has been married to this concept. Invisible barriers have been broken down. Each problem is a holistic problem – not a stove pipe. We tackle everything together.
Focus on Speed, Accuracy Quality
AoP helps keep us on track to meet our customers’ needs. Never before have we had a clearer picture of how we impact speed, accuracy and quality in every phase of our processes. Now that we have this visibility and the tools and resources available to improve, it is our responsibility to act.
As we continue to fully adopt AoP and our automated systems, CCAD will become an evolving machine of efficiency, increasing our process stability, surge capability and materiel readiness at the point of need. This should posture us for opportunities to expand our capabilities and take on additional work in the future. By developing a stable and synchronized force today, we are rewriting materiel support readiness through optimization across the enterprise for years to come.
CCAD makes Army aviation readiness its top priority as the Army’s trusted organic industrial base for helicopters and their components. With enduring support to U.S. Army Aviation and Missile Command and Army Materiel Command, the team at CCAD is ready to contribute to the Nation’s security.
COL Allan H. Lanceta is the commander of Corpus Christi Army Depot and Brigitte Rox is a CCAD public affairs specialist; both are located at Corpus Christi, TX.