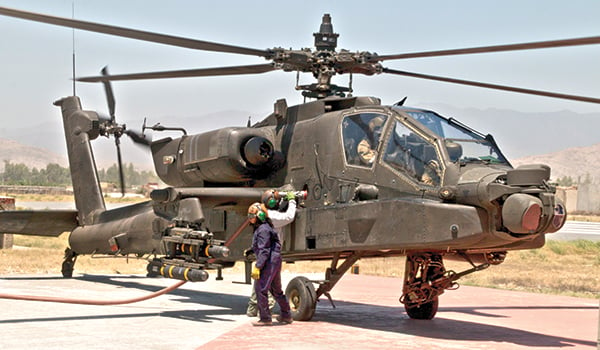
By LTC Joseph M. Herman with Mr. Oswald Ingraham: An AH-64E Lot 4 enhanced aircraft was enroute from Redstone Arsenal, Alabama to Mesa, Arizona when the aircraft transmitted a message to the monitoring ground personnel that the LINK 16 battery was low. If the LINK 16 battery fails, the LINK 16 Line Replaceable Unit (LRU) must be returned to the original equipment manufacturer (OEM) for repair. A Problem, Plan, Part, People, Time and Tool (P4/T2) analysis was conducted while the aircraft was in flight allowing Boeing to check their stockage for batteries and prepare to replace the low battery upon aircraft arrival. The Apache Project Management Office (PMO) validated the availability of LINK 16 batteries with the Defense Logistics Agency (DLA) in case no batteries were on hand at Boeing while the aircraft was enroute to its final destination.
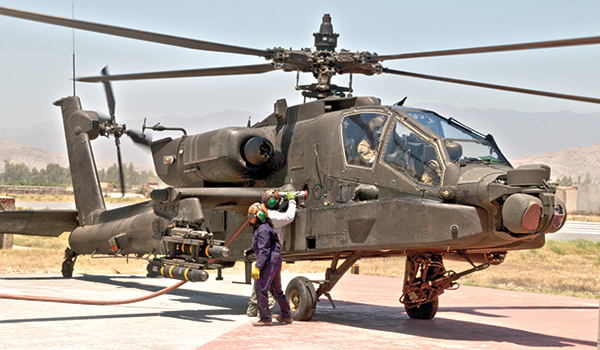
An AH-64 Apache helicopter hot refuels at Forward Operating Base Fenty, Afghanistan, May 21, 2016. A team of California and Washington Army National Guard Soldiers from the 40th Combat Aviation Brigade provided the refueling support. / U.S. ARMY PHOTO BY SSG IAN M. KUMMER, 40TH CAB PUBLIC AFFAIRS
An AH-64E Version 4 aircraft transmitted to the ground monitoring organization a failure of the Embedded Global Inertial (EGI) number 1 and an issue with the Backup Control System (BUCS) upon landing at a remote site. The ground crews performed a P4/T2 analysis of the aircraft problems. This includes an evaluation of the landing site and roads that may be used for a pending recovery mission, if required, via map location information supplied by the Smart Tools for Aviation Maintenance Picture (STAMP) ground station dashboard, prior to the pilots performing their shutdown of the aircraft at the remote landing spot.
An AH-64E Version 4 aircraft transmitted an alert to the production control office that the Mission Processor (MP) number 1 had failed during a mission. Production control was able to perform a P4/T2 analysis of the situation while the aircraft was inflight to insure the parts, people, and technical expertise was waiting for the aircraft to land instead of waiting for the aircraft to return and then start the maintenance evaluation process.
Apache maintenance science fiction? No, this is Apache maintenance science fact with the fielding of System Level Embedded Diagnostics (SLED)/STAMP.
How We Got There
The Apache Product Office, Aviation Engineering Directorate (AED), and OEMs were not receiving data from the newly fielded AH-64D aircraft to support product improvements. Some data received was paper based Standard Army Management Information System (STAMIS) information. Data was being collected by paper-based data systems and collectors in the field. The initiative to receive near real time actionable data from the platform for analysis, product improvements, and reducing the maintainer’s burden started in 2003. The Apache PMO partnered with Task Force 160 to convert the paper logbook to the Task Force 160 Electronic Logbook System (ELAS). Electronic logbook data was sent to Apache PMO, AED, and OEMs from units to support the recapitalization of component improvements.
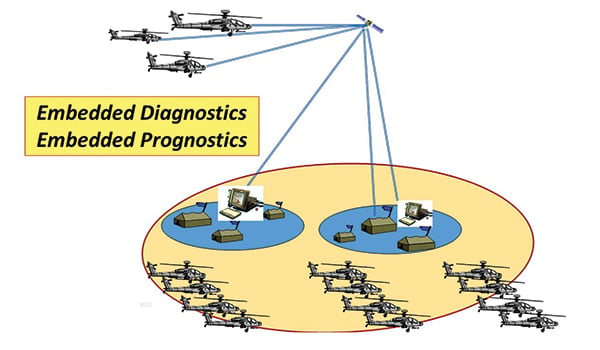
Phase maintenance intervals could not be improved because phase inspections were paper- based and out of the material developer’s information chain. After the completion of a phase inspection the completed phase books were sent to Corpus Christi Army Depot (CCAD) and destroyed six months later. Apache PMO used another Task Force 160 product, the Integrated Maintenance Phase System (IMPS), and deployed the system with training to six AH-64D battalions. Digital collection of phases and the evaluation of phase maintenance actions by AED lead to extending the AH-64D phase interval from 250 to 500 hours, effectively doubling the bank time of Apache battalions. These digital maintenance systems were selected to become the new Army STAMIS, Unit Level Logistic System-Aviation (Enhanced) (ULLS-A (E)).
As the digitization of Army maintenance continued, Apache PMO recognized a need to transmit platform data from the aircraft to the maintainers for quicker responses in a challenging maintenance environment. The Common Logistics Operating Environment (CLOE) was the Army Campaign Plan initiative to synchronize logistics concepts, organizational approaches, information, and a new generation of technologies into a single operational and technical architecture for current and future force structures. The goal was increased mission readiness, improved situational awareness, and lower costs for sustaining Army equipment. The AH-64D was selected as the platform to support the CLOE Proof of Concept (PoC).
Through collaboration with Dr. Miranda Keeney, U.S. Army Logistics Innovation Agency (LIA), Apache was provided with Very Small Aperture Terminals (VSAT) and Combat Service Support Automated Information System Interface (CAISI) for a field test with an operational unit (1-4 Cav, Ft. Hood, TX).
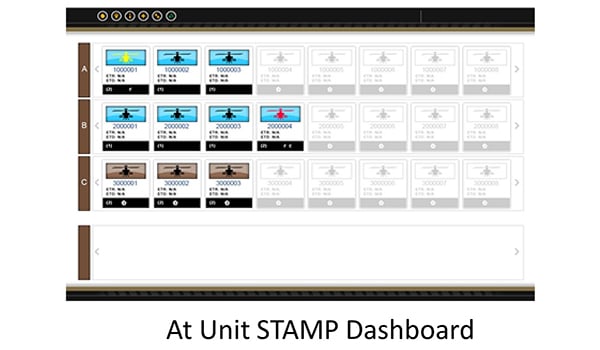
The test demonstrated the automatic transmission of STAMIS, Maintenance data recorder (MDR) and Modernized Signal Processor Unit (MSPU) data from a wireless enabled battalion of aircraft logbooks in a field environment to an Apache PMO dedicated server collection point at Redstone Arsenal AL. This is now known as the Joint Aviation Technical Data Integration (JATDI) Top Tier Server.
Due to the success of this PoC the basis of issue for VSAT by the Force XXI Battle Command, Brigade-and-Below (FBCB2) project office was increased from one VSAT per battalion to five per battalion with the maintenance organization having its own dedicated VSAT for STAMIS logistic connectivity and a data flow from the aircraft logbook to the JATDI Top Tier server once the logbook is connected to the VSAT via CAISI wireless or wired network connections.
SLED/STAMP with Interactive Electronic Technical Manual (IETM) Integration
Apache PMO understood Real Time versus Near Real Time awareness of in-flight faults would greatly reduce the maintenance operational response time and increase logistics situational awareness. The AH-64E V4 and V6 have this capability embedded to accomplish self-diagnosis to provide a system level health assessment via on-board processing that can be transmitted via the Blue Force Tracker II (BFT II) network to the unit’s production control.
Since the Vietnam War, maintainers could not begin planning their work to fix an inflight fault until the aircraft returned and faults were entered into the aircraft logbook after landing. The Development and Modernization Product Manager’s Office, with Steve Sutherland as the Apache SLED Team Lead, deployed the SLED/STAMP system to Eglin Air Force Base, Florida in August 2014 for the Follow-on Operational Test and Evaluation (FOTE) with outstanding success.
The STAMP dashboard changes to reflect the aircraft’s current status so the maintainers can quickly see Warnings, Cautions, Advisories, Faults and Exceedance’s (WCAFE) as they occur on an aircraft. It can also distinguish between an aircraft that has landed at home versus an aircraft that has been forced to perform a precautionary landing. From the Dashboard, the maintainer can easily delve deeper into the full SLED report to gain detailed information regarding the WCAFEs. The information transmitted real time during the flight includes the time the fault was detected and logged to the Aircraft Maintenance Data Recorder (MDR) and current detected WCAFES that are detected and displayed to the crew. Faults transmitted from the aircraft to the STAMP dashboard is linked to the IETM for rapid evaluation of the fault by the maintainer, insuring the P4/T2 analysis is conducted and the unit is ready to respond upon the return of the aircraft or recovery.
recautionary landing location is transmitted to the STAMP dashboard ensuring the maintainer can evaluate the area for access, security considerations, and downed aircraft recovery planning while ensuring maintenance personnel have the information to support recovery operations. All of this information is provided real time allowing maintainers to streamline the P4-T2 maintenance management process.
As demonstrated during FOTE and subsequent missions, STAMP has the potential to optimize aircraft turnaround time utilizing real time fault data from the aircraft in flight. Potentially STAMP will save maintainers hours of non- and partially mission capable time by quickly determining resources required to energize the logistics planning process while an aircraft is inflight.
In addition to the desktop application, the Army is also developing a cross platform solution that will have the capability to support mobile devices running Android and iOS. This mobile proficiency will enhance STAMP’s capacity to provide the Apache aviation maintenance community with access to near real-time information for aircraft maintenance resulting in a streamlined maintenance logistics footprint and most importantly the ability to quickly return an aircraft to an operational status.
STAMP gives maintainers a head start never before experienced in Army Aviation. As stated by one maintenance noncommissioned officer at the FOTE test event, “I wish we had this at the unit now.”
LTC Joseph Herman is the product director for the Apache Development and Modernization Office in the Apache Project Office and Mr. Oswald (Oz) Ingraham is the logistics/sustainment lead assigned to support the Development and Modernization Product Office; both located at Redstone Arsenal, AL.