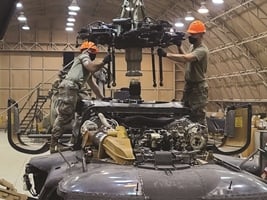
Aviation Branch Maintenance Officer Update – By CW5 Patrick O’Neill
As units return from a reduced operational period over the holidays, maintaining aircraft readiness can be challenging. With reduced manpower, typical winter weather, and the current COVID-19 supply-chain disruptions, having a maintenance strategy to bridge these sustainment gaps and meet the eventual surge of flying hours is critical. What is also critical, but a little more opaque, is a strategic view on maintaining current and future fleet aircraft in Large Scale Combat Operations (LSCO) in a Multi-Domain fight. As we modernize our enduring aviation fleet and prepare for Future Vertical Lift (FVL), understanding how to apply modernization efforts and the Army Aviation Enterprise Sustainment Strategy at the tactical- and operational-maintenance levels is critical for our future fight.
Maintainers that turn wrenches and maintenance managers who advise and schedule aircraft must have a clear understanding of how maintenance will be conducted for LSCO, and what modernization efforts are currently ongoing. Developing this interconnected knowledge of strategy and modernization will reduce the learning curve when it comes to the application of these systems in LSCO. Some of the modernization efforts include Advanced Manufacturing, Prognostic and Predictive Maintenance (PPMx), and using sensored parts that reduce time between overhauls and enable extended Maintenance Free Operating Periods (MFOP). These are all eventualities that will reside in a maintainer’s toolbox in the not too distant future.
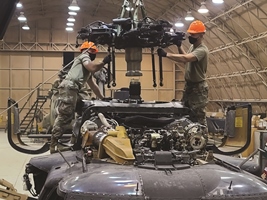
The Army and other services are actively pursuing advanced manufacturing (AM) solutions. Of course, along with this new ability there are policies in place to help guide us in the proper use and application. Under the current policy, all AM parts must be approved before use. Three-D printed parts may look and fit as well as the original, but they may not perform the same. U.S. Army Aviation and Missile Command (AMCOM) Policy 070-062 and AMCOM Execution Order 050-18 outline that guidance.
The AMCOM policy states that units have input into nominating which parts are evaluated for 3D scans first. Currently, most of these solutions are made above the brigade level, but the eventual focus is to get some level of advanced manufacturing to the maintainers in the field. Being able to produce a low-density part that can be used to extend operating periods or recover an aircraft forward in combat at the battalion- or company-level is something for which we should continue to strive.
The starting block of this comes from developing 3D models of current aircraft within the fleet and any future fleets with FVL. In partnership with academia and, in particular, the National Institute for Aviation Research at Wichita State University, we have completed a 3D model of a UH-60 in the past few months. We will eventually have every aircraft 3D modeled and those scans will be available for the maintainer to use.
The 3D modeling of parts and components opens the doors of possibility to a fully printable system. The reality might be a portion of a system, or a reinforcing part derived from a maintenance engineering call. As maintenance managers or maintainers, how will this change or influence operations? Currently, there are several units that have purchased, or are in the process of purchasing, the most basic 3D printers to start manufacturing approved, non-flight critical parts and tools. The list of items will only continue to increase. Sophisticated printers will be able to produce more complex components. One day in the near future, units will be able to produce limited critical flight components. The National Guard has already started to produce several components with 3D printers within the Aviation Classification Repair Activity Depots. Understanding how to safely and effectively employ the use of advanced manufacturing in the future will enable units to extend their reach and lethality while operating in contested environments, across dispersed footprints, for longer periods of time.
Prognostic and Predictive Maintenance (PPMx) is a key component to managing and maintaining the current and future fleet of aircraft. Past health monitoring units may have only measured vibrations, but current and future systems will create an interconnected catalogue of sortable data that can be used to efficiently manage aircraft by the tail number as opposed to by fleet. PPMx will allow for longer intervals between scheduled maintenance actions and can be individualized for specific aircraft. More importantly, PPMx will allow commanders and maintenance managers the ability to see what is going to fail next and address impending failure on components prior to the time between overhauls or well after the recommended hours for service. This will eliminate unnecessary preventive maintenance. By sustaining aircraft MFOP utilizing PPMx with a common health indication data architecture across all fleets, and implementing tail number-based decisions, we will minimize risk and reduce maintenance man hours and authorized stockage list, while also extending operational reach and duration.
By having well-managed fleets with long MFOP, we will greatly reduce the parts needed to maintain these aircraft. PPMx will help us with this task by predicting only what’s needed, thus reducing our logistical footprint. We are increasing capabilities with 3D printing and additive manufacturing to produce parts that are needed, which improves our operational availability and increases are organic capabilities. Lastly, PPMx will decrease life-cycle cost of our airframes by reduced maintenance on wing of removal and replacement of parts that still have useful safe-operating time left.
How we use and implement these tools and systems will make the difference in winning in LSCO – and winning matters.
—–
CW5 Patrick O’Neill is the Aviation Branch Maintenance Officer, U.S. Army Aviation and Missile Command at Redstone Arsenal, AL.