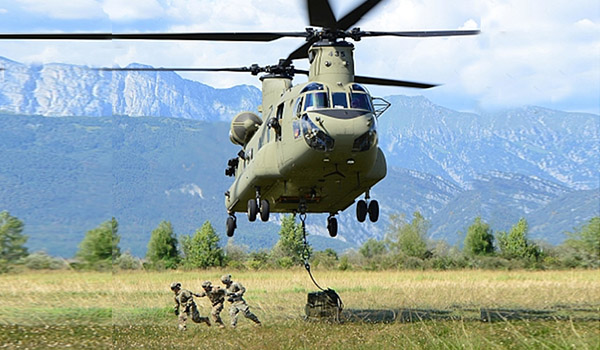
CCDC Avn Tech Talk / Dr. Thomas L. Thompson: The Army’s next generation of rotorcraft will fly significantly faster and farther than our current fleet, but they will continue to perform missions that require them to takeoff/land vertically and hover out-of-ground effect (HOGE) at high altitudes for extended periods of time.
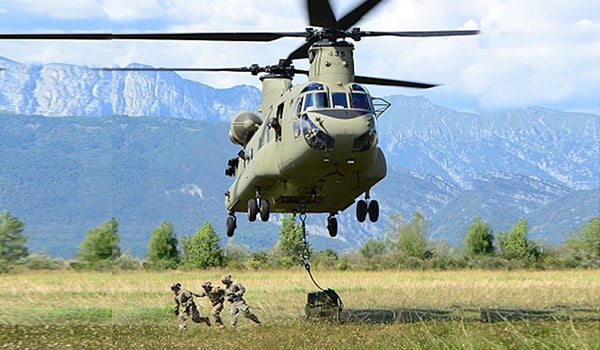
CH-47F hovering at high-altitude./ U.S. ARMY PHOTO
While the need for increased speed and range will change the look of Future Vertical Lift (FVL) aircraft, the unchanging requirement for HOGE capability will dictate (from an efficiency standpoint) that they remain rotorcraft – aircraft that generate vertical thrust more efficiently than other VTOL machines by using large rotors to accelerate (or induce) a large mass of air at a relatively low velocity. As the Army presses forward with these advanced designs, we must continue to pay close attention to defining, designing and demonstrating that most distinguishing characteristic of a rotorcraft – its ability to hover efficiently.
As industry strives to meet the Army’s challenging requirements for high-speed flight, aviation program offices must continue to establish and enforce hover performance requirements for new or modified aircraft. The user must be closely involved in defining requirements for hover takeoff gross weight (or payload), pressure altitude, and temperature. For most Army programs, the design requirement is to hover out-of-ground effect (i.e., taking no credit for the beneficial effect of the “ground cushion” on power required) for the primary mission gross weight at 4000 feet, 95 degrees F ambient conditions. Users may also specify a vertical rate of climb at these conditions, typically 500 feet/minute, to provide some margin in satisfying mission requirements.
FVL aircraft rotor designers are assimilating hover and high-speed flight requirements to develop a system that satisfies requirements in both regimes. Informed by results of aerodynamic analyses and wind tunnel tests, designers are defining the blade airfoil geometries, adding twist and taper to the blades, and shaping the blade tips to ensure that the power required to produce hover lift (induced power) and spin the blades (profile power) is within the limits of installed engine power available. These choices for hover are balanced, however, with the often-conflicting aerodynamic requirements for high-speed flight. For example, while a rotor with highly twisted blades is best for hover, it will likely reduce forward flight performance and increase aircraft vibration. Similarly, while a rotor blade having a relatively small chord length will reduce profile power in hover, the blade area may not be sufficient to generate the lift needed to maneuver in forward flight.
As FVL designs are finalized, Army and industry engineers will prepare to conduct flight tests to demonstrate the airworthiness and performance of the new aircraft. To fully demonstrate HOGE capability, the test team will arrange for testing at a high-altitude test site, where the rotor can be tested at conditions more representative of performance specification requirements. To ensure the accuracy of the collected data, the test team will calibrate instrumentation to measure engine torque, rotor shaft torque and the load on the cable that tethers the hovering aircraft to the ground (use of a tether cable allows for testing at thrust levels greater than that required to balance the weight of the aircraft). The test team will also set up a weather station at the test site to measure ambient pressure, temperature, and winds at the same height above ground as the hovering helicopter.
As testing is conducted, engineers will carefully review the hover test data to confirm its accuracy and repeatability. Some amount of data scatter is expected but will be minimized by using the measured wind data to exclude test points that are not representative of hovering flight (winds of three knots or less are normally required for performance data). A final data set, approved by Army engineering and program offices, will then be used to assess compliance with specification requirements and to develop hover performance charts for the aircraft Operator’s Manual. Pilots of Army helicopters depend on these charts to specify the maximum load they can pick up at a given location.
Commitment and attention to detail from all parties – users, program managers, designers, and testers – are needed to ensure that our next generation of aircraft continue to meet the requirement that is fundamental to the purpose and practicality of a rotorcraft.
Dr. Thomas L. Thompson is the Chief Engineer for Aeromechanics in the Systems Readiness Directorate at the U.S. Army Combat Capabilities Development Command, Aviation and Missile Center, Redstone Arsenal, AL