
AMCOM Commander / By MG James M. Richardson: The Future Vertical Lift (FVL) effort is gaining momentum across the Army and across the Department of Defense (DoD). It may be unprecedented in DoD procurement to have such a wide range of aviation users come together to participate in the development and acquisition of a family of systems.
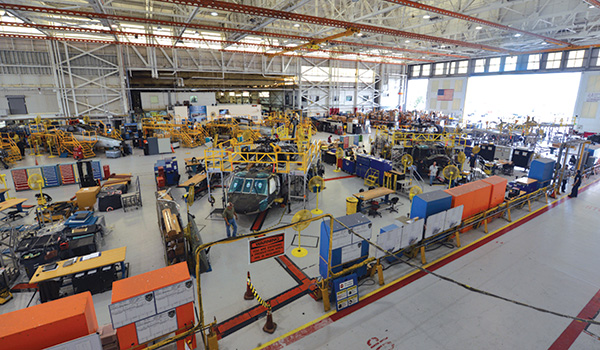
The H-60 rebuild line at Corpus Christi Army Depot (CCAD). Army Aviation must leverage its knowledge of current system performance to build affordability into future aircraft designs. / U.S. ARMY PHOTO BY CCAD PUBLIC AFFAIRS
All DoD Services are contributing to the capabilities of these new systems, the missions they’ll perform, and of course, their cost. I advocate that our Branch and Community collaborate on building affordability into FVL now, as concepts and designs take shape. Naturally, no one knows at this stage what the variants of FVL will eventually cost, but before those of us in the Aviation Enterprise get much further, it would be well to remember that whatever size check is written to purchase say, a utility FVL variant, that check will just be the initial outlay.
Follow-on Costs
Traditionally, the procurement costs are about 30% of the total life cycle cost. Historically, a procurement dollar is followed, in the Army, by about $2.00 to $2.50 in operating dollars before that helicopter is retired (or more likely, rebuilt). Let’s assume an FVL variant for the UH-60 is approved; one that complements the current family of UH-60. It will be more capable and therefore will probably cost more. Just to make it easy to compare, let’s assume the last delivered new UH-60 arrives at Fort Campbell costing $24M. Being optimistic, let’s further assume the more powerful, faster, survivable FVL utility version arrives the next year at a cost of $35M.
The Army will likely spend over $40M operating that UH-60 during its life cycle and if the pattern holds true, our hypothetical FVL version will be over $60M. Those expenses won’t be shouldered by the acquisition community alone. The Aviation Center at Ft. Rucker, the Army Materiel Command, and especially our aviation units will be paying these bills. There is no reason to believe future operation and maintenance accounts will be any more robust than they are now, so if new systems are even more expensive to operate, we will only add additional strain on budgets and perhaps limit available flying hours.
Total Ownership Costs
But what if we recognize those total ownership costs up front? Total ownership costs are tricky to forecast for any new mission design series (MDS) precisely because it is new. Typical cost estimates for new systems tend to be optimistic, not necessarily because of intentional bias, but because we don’t know what we don’t know. Eventually, new MDS operation & sustainment (O&S) costs will be recognized even though they are distributed across multiple organizations.
Budget pressures tend to make comparatively expensive aviation systems stand out from other Army equipment. So how do we get ahead of the FVL O&S cost curve and bend it down?
We won’t know everything about operating and maintaining an FVL fleet ahead of time, but there is much we do know from decades of flying our legacy fleets. For instance, it would be a challenge, but it is well within our ability to do comprehensive comparative analyses across the existing fleets to select “best of breed” solutions. For example, which would be preferable, strap packs or elastomeric bearings? What have we learned about mechanical vs. electrical drive? What are the long term cost considerations for composite blades compared to alloys? There are other examples, but you get the idea. Let’s roll into FVL with a solid grasp of our current strengths in design, and carry these forward in analysis of alternatives.
We have also learned much about the effects and high costs associated with corrosion. The Army has spent millions of dollars in repairs that could have been avoided if more consideration had been applied to corrosion control in the design and selection of materials used in our fleets. Let’s analyze what we’ve learned, see what we can apply to FVL, and include this in the requirements.
Another area for cost control analysis will be the Core Depot Assessment. By statute, half of depot-level support for any system, including FVL, must be organic. To ensure successful development of the organic industrial base supporting FVL, we must protect the government’s proprietary rights to the technical data. Availability of technical data will increase cost competition both from an organic and industry participation perspective. Without such access, O&S costs are very difficult to influence.
Cost of Ownership IPT
The requirements, acquisition, science & technology, and commonality Integrated Process Teams (IPTs) working FVL are already transforming ideas into reality. Certainly, affordability is under consideration by all four IPTs. Reliability, sustainability, and maintainability are part of the equation and directly impact the eventual cost of ownership. I believe that the user community would be well served if we added a ‘cost of ownership’ IPT to the effort. This IPT would have a singular focus – to ensure the long term cost of operating the FVL family will be one that our nation can afford over a 50 year lifespan. Today’s aviation enterprise can draw on years of experience supporting both peacetime and war. Let’s capture that knowledge to influence and inform the requirements and design processes. We must ensure the cost of flying missions doesn’t limit the hours available to student pilots, sideline aviation assets in combined arms training, or exacerbate support requirements in theaters of operation. As a bonus, if operating the fleet costs less, we can be assured that a byproduct will be more time on wing, whether at the schoolhouse, at home station or in the middle of a firefight.
The next couple of years will be exciting times for rotary wing aviation as industry partners roll out technology demonstrators. These will provide real world hardware to help evaluate what is in the realm of the possible. While current and future aviators look at the sleek designs and think up even more “what if we could” capabilities, let’s work together as an enterprise to get affordability decisions properly researched, vetted, and included before we even get to Milestone A.
MG James M. Richardson assumed command of the U.S. Army Aviation and Missile Life Cycle Management Command at Redstone Arsenal, AL on June 12, 2014.