
AMCOM / By CSM G. Mike Dove: If you attended AMCOM 101 or the AAAA Cribbins Symposium in Huntsville, then you probably heard MG Gabram talk about the supply chain and how we at the U.S. Army Aviation and Missile Command (AMCOM) acquire parts in order to build strategic depth.
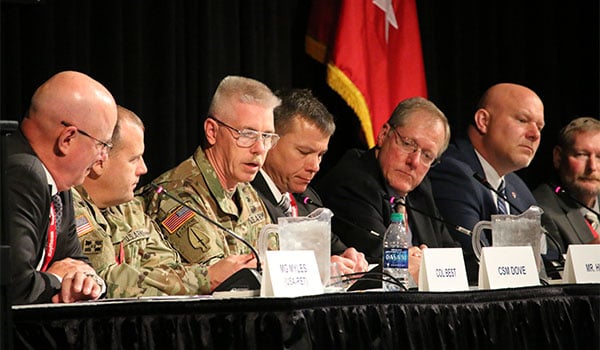
CSM Mike Dove makes a point during the AMCOM Optimizing Maintenance Panel of the Joseph P. Cribbins Aviation Product Sustainment Symposium, Nov. 13, 2018 at the Von Braun Center, Huntsville, AL. / U.S. ARMY PHOTO BY TOM VOIGHT, PEO AVN
AMCOM identified at least 10 parts as readiness drivers on each of the helicopter platforms. These are items that we have to watch closely and intensely manage in order to provide these parts at the time of need. We have three ways to acquire these parts: commercial buy, commercial repair, or organic repair. Some of the unexpected events that have a significant impact on the supply chain are hail storms, hurricanes, and birds activating fire suppression systems. All of these events take a toll on the supply system and impact the expected delivery dates of parts.
COSIS Program
I want to add another dimension that factors into the supply chain where our maintainers and logisticians have a direct impact. What happens to the parts once they are delivered? I am referring to the large parts such as engines, blades, rotor heads and transmissions which are usually stored outside due to their size. Does your unit have a Care of Supplies in Storage (COSIS) program? Does your combat aviation brigade (CAB) have adequate storage facilities in the supply support activity (SSA) to store those large and very expensive items? What about when they are issued from the SSA to the battalions? Does the battalion tech supply have the storage capacity for those types of items, or are they placed outside again? How often are those items inspected at your installation? How often should they be inspected, and who has the responsibility to inspect those items? The U.S. Army has an incredibly expensive problem with corrosion of at least $1 billion per year. At times corrosion is found on new parts still in the shipping container sitting in the SSA or at the battalion tech supply. In 2013 we found over $36 million worth of parts, in one CAB, which were corroded due to improper storage and lack of routine inspections.
Check your SSA, tech supply and unit SOPs to ensure these items are being inspected and corrective actions are taken to reduce this loss. Most of these large containers have humidity indicators on them which are supposed to be blue when it is good and white when the humidity inside the can exceeds a certain level. The short amount of time spent checking these indicators on a frequent and regular basis can save the Army several million dollars on repair parts in Army Aviation alone.
Cribbins Highlights
At the Nov 2018 Cribbins event we talked about maintenance on our current fleet, a path forward with our future vertical lift (FVL) platforms, future capabilities and condition based maintenance (CBM) on our current platforms. The goal for maintenance intervals on the FVL platforms is 30 days and 60 hours without touching the aircraft. That sounds like a lofty goal, but think about the commercial airline fleet. How often do they de-panel an airliner to inspect before the next flight?
I discussed the newly published TC 3.04-71 Aviation Maintenance Training Program (AMTP) and some opportunities we may have with regard to synthetic training devices to enhance maintenance training. The Western Army Aviation Training Site in Arizona has one such solution for the LUH-72. They have a digital maintenance trainer which allows National Guard maintainers to virtually remove and reinstall parts on the aircraft. The NCOs set up and supervise each task the maintainer needs to learn or possibly re-train to gain proficiency. They have the ability to practice maintenance tasks on the computer multiple times before they ever actually touch an aircraft. This improves proficiency and reduces accidental damage to the aircraft.
Mr. Brad Oxenford shared some solutions Columbia Helicopters is doing with their commercial fleet of 234 Chinook and Vertol 107-II helicopters. These are commonly referred to in the military as the CH-47 Chinook and CH-46 Sea Knight. In various locations around the world, Columbia Helicopters has a requirement to fly their helicopters as high as 100 hours per month. In order to meet this high demand, Columbia Helicopters reorganized the inspections normally conducted during the phase maintenance interval. This relatively simple adjustment allows them to meet their mission of providing rotary wing support. In contrast, if the Army flew the CH-47 fleet 100 hours per month, we would perform a phase maintenance inspection every third month, or four phases a year per airframe.
I shared what we are doing in the Aviation Branch with tracking the maintenance tasks and capabilities of our aviation maintainers. TC 3.04-71 AMTP was published in July 2018 and will go fully operational capable in FY21. As a branch, we have not done a good job of keeping track of the skill sets or our maintainers. Usually when a newly assigned Soldier or NCO arrives at a unit, they are placed either in a maintenance or flight position based on their rank. Most of the time we assume an NCO has conducted phase maintenance inspections, and that may not be the case. The bottom line is we need to do a much better job of managing the talent and skills of our Soldiers. With the use of the AMTP we can manage that talent much better as well as assist Soldiers and NCOs in gaining accreditation for Airframe and Powerplant ratings.
Overall the Cribbins Symposium was a success and continues to bring the Aviation Enterprise together to share ideas and provide solutions to the Warfighter. It will be interesting to see how aviation maintenance will evolve over the next few years.
Tradition of Excellence!
CSM G. Mike Dove is the command sergeant major of the Aviation and Missile Life Cycle Management Command at Redstone Arsenal, AL.