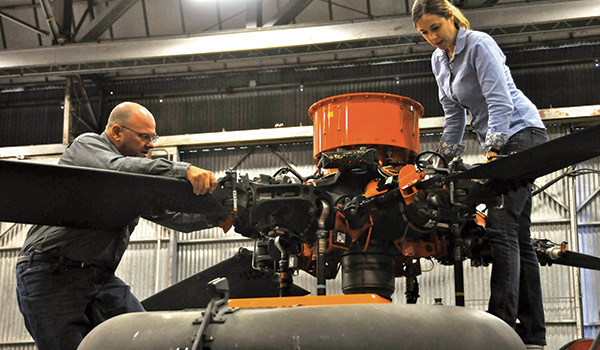
Research& Development – Science & Technology / By Dr. William D. Lewis: During our operational duty assignments as Army Aviators, our ability to safely and effectively accomplish flight missions results from the coalescence of numerous factors: equipment, training, teamwork, leadership, etc. One of the foundational aspects contributing to our mission success is the extraordinary scientific and engineering talent that resides in our government engineering organizations, the aircraft and aviation systems industry, and academia.
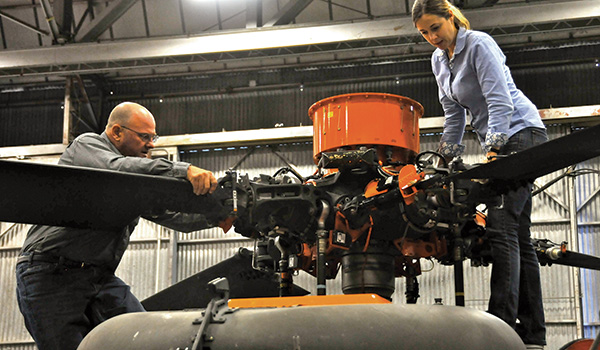
Mr. Kevin Kalinowski and Dr. Christina Ivler inspect the laser measurement system mounted on an AFDD flight research aircraft. / AMRDEC ADD IMAGES
However, until one enters the research, development, test, and evaluation community, it would be difficult to fully appreciate the breadth and depth of engineering expertise found throughout our Army Aviation materiel enterprise. Toward that end, I’d like to take this opportunity to introduce Army Aviation readers to a few representative members of the Aviation Development Directorate’s (ADD) exceptional technical workforce.
With our headquarters at Redstone Arsenal, Alabama, ADD is a component of the U.S. Army Aviation and Missile Research, Development, & Engineering Center. We conduct the majority of the Army’s science & technology (S&T) work in support of vertical lift aviation capabilities. ADD is comprised of the Aviation Applied Technology Directorate (AATD), located at Joint Base Langley-Eustis (JBLE), Virginia, and the Aeroflightdynamics Directorate (AFDD), co-located with NASA Research Centers at Moffett Field, California, and JBLE, Virginia. Our combined workforce of nearly 400 people includes military personnel, government civilians, and support contractors.
Rotor-state Feedback Control System Development
Dr. Christina Ivler is the Principal Investigator for this flight test demonstration project. Rotor-state feedback, or the feedback of the tilt of the rotor-disk through the control system to the swashplate, provides improved performance of fly-by-wire control systems. By measuring the motion of the rotor, it is possible to sense and respond to atmospheric disturbances quickly, thereby reducing the resulting motion of the fuselage by 30-40% as compared to a standard fuselage feedback control. This information improves the pilot-vehicle system’s ability to tightly track commands during turbulence and provides reduction of rotor flap motion, which is associated with reduced structural loads.
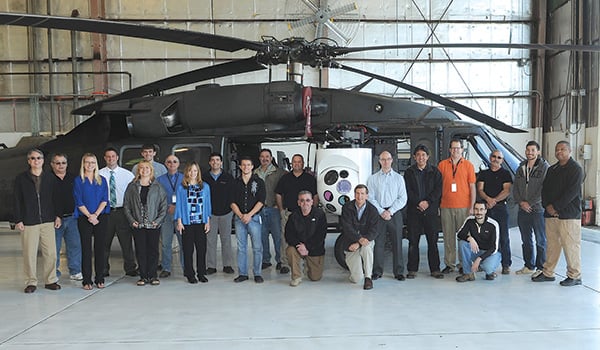
Mr. Jerry Clifford, Mr. Corey Barton (7th and 8th from the right), and fellow members of the AATD ARMS Team surround the installed system between qualification test flights.
Dr. Ivler has supported Army flight control research at AFDD for nearly 8 years. She was recently appointed as a senior subject matter expert in advanced flight control systems. In her off-duty time, she also works as a professor at Santa Clara University, where she teaches undergraduate and graduate level dynamics and control courses. Dr. Ivler is testing the rotor-state feedback technology on a JUH-60A helicopter modified with a fly-by-wire flight control system. During this project, she will demonstrate and quantify improvements in stability and handling qualities in winds and turbulence by leveraging rotor-state feedback.
Electro-Optic (EO)/Infrared (IR) Signature Characterization
Mr. Jerry Clifford, a mechanical engineer, leads aircraft survivability technology development projects and is the overarching project lead for all of AATD’s EO/IR signature measurement flight test activities. Mr. Cory Barton, an electrical engineer, supported the survivability technical area as project lead for the Airborne Radiometric Measurement System (ARMS).
High resolution, multi-spectral signature measurements are required to accurately characterize rotorcraft susceptibility to threat antiaircraft weapon systems. To meet this requirement, Mr. Barton, Mr. Clifford, and the aircraft survivability team developed ARMS, which is capable of collecting in-flight measurements in spectral bands of interest. The calibrated ARMS hyper-spectral capability provides detailed, high resolution spectral and imagery data of rotorcraft signatures.
The ARMS sensors are housed in a wing-mounted gimbal system on a UH-60 aircraft and are controlled by operators within the cabin. ADD’s Survivability Technical Area Team conducts measurements using ARMS while also developing signature management and survivability planning technologies including adaptive engine suppressors, in-flight, real-time route optimization systems against pop up threats, and signature reduction coatings/technologies. These efforts are coordinated with the Army Aviation and Joint survivability communities to provide effective, balanced, and affordable aircraft survivability solutions in signature management, aircraft survivability equipment, and vulnerability reduction.
Combat Tempered Platform
Mr. Nate Bordick is ADD’s Lead for the Structures Technical Area. He has earned engineering degrees from both Pennsylvania State University and Old Dominion University. He has over 14 years of experience at AATD leading structures S&T projects focused on reducing structural weight and improving durability and reliability.
Mr. Bordick leads a research and development project to explore integrated technology solutions that harden, or combat temper, Army rotorcraft, enabling the aircraft and crew to stay in the fight for extended periods and working towards a “zero-maintenance” vision.
The Combat Tempered Platform Demonstration (CTPD) is a collaborative effort with the Sikorsky Aircraft Corporation to demonstrate an integrated platform solution for the UH-60 Black Hawk that exemplifies both operational durability and total survivability. Six technology areas that comprise the system level solution were carefully selected, matured, and demonstrated through full-scale structural, ballistic, crash, and flight testing. These areas are: durable airframe, fire management, vibration reduction, rotor durability, crashworthiness, and flight control laws. The end product of Mr. Bordick’s and the CTPD team’s work in this area will be a revised system specification for the UH-60.
Future Affordable Turbine Engine
Ms. Anastasia Kozup holds engineering degrees from both West Virginia University and George Washington University. She is senior member of the Engines Technical area and serves as the project lead for several engine system demonstrator programs, including the Future Affordable Turbine Engine (FATE) effort with General Electric.
FATE is an S&T engine demonstrator effort aimed at developing advanced turboshaft engine technology in the 5,000 to 10,000 shaft horsepower class for primary application to current and future Army rotorcraft. The goals of the program include a 35% reduction in specific fuel consumption, an 80% improvement in horsepower-to-weight ratio, and a 45% reduction in production and maintenance costs compared to current engine technology.
The FATE program was awarded to General Electric Aviation in 2011 with a demonstration plan that incorporates multiple component tests and two full engine system demonstrations to achieve a readiness level appropriate for technology transition. The improved fuel consumption, durability, reliability, and maintainability characteristics and the emphasis on lower production and maintenance costs would yield significantly reduced operations and sustainment costs.
Joint Multi-Role (JMR) Technology Demonstration (TD)
Mr. David Friedmann leads the government’s core team for the JMR air vehicle demonstration (AVD). He and project engineers Clay Ames, Nelson Ciron, John Crocco, and Matt Spies manage all the milestones in this very dynamic effort. Aided by the government’s program management efforts, two industry partners quickly moved past the initial design phase and into final detailed design and subsystem fabrication for their TD aircraft.
Many of the aircraft components, including fuselages, are in final stages of buildup and testing. The two aircraft will begin assembly early in 2016. Both TD aircraft are targeted for their initial flights in 2017. Additionally, the AVD team successfully developed plans and garnered resources to continue technology maturation with two other AVD industry partners.
In addition to the AVD, the JMR TD program team has also been extremely busy executing the mission systems architecture demonstration (MSAD). Mr. Marty Walsh leads the MSAD effort. As part of the MSAD, a Joint Common Architecture demonstration was recently completed and proved hugely successful in validating the concept of efficient integration of software portable units into variations of hardware and operating environments. The next step is a more complex and integrated effort called the Architecture Implementation Process Demonstration, which will be executed in the 2016-2017 timeframe to shape government and industry understanding and competencies with the ultimate goal of an efficient, effective, enduring, and affordable platform architecture.
Engineering the Future
Within the constraints of this short article, I have only introduced you to a few representative members of ADD’s exceptional technical workforce, and highlighted only a few of our ongoing S&T projects. Be assured that there are many other talented engineers who are hard at work on many other groundbreaking research and advanced technology projects that will substantially benefit Army Aviation in the years ahead. Our shared goal is to enable safe and effective Army Aviation operations with the highest possible aircraft performance and dramatically enhanced supportability.
Dr. William D. Lewis is the director of the Aviation Development Directorate of the Aviation and Missile Research, Development, and Engineering Center located at Redstone Arsenal, AL.