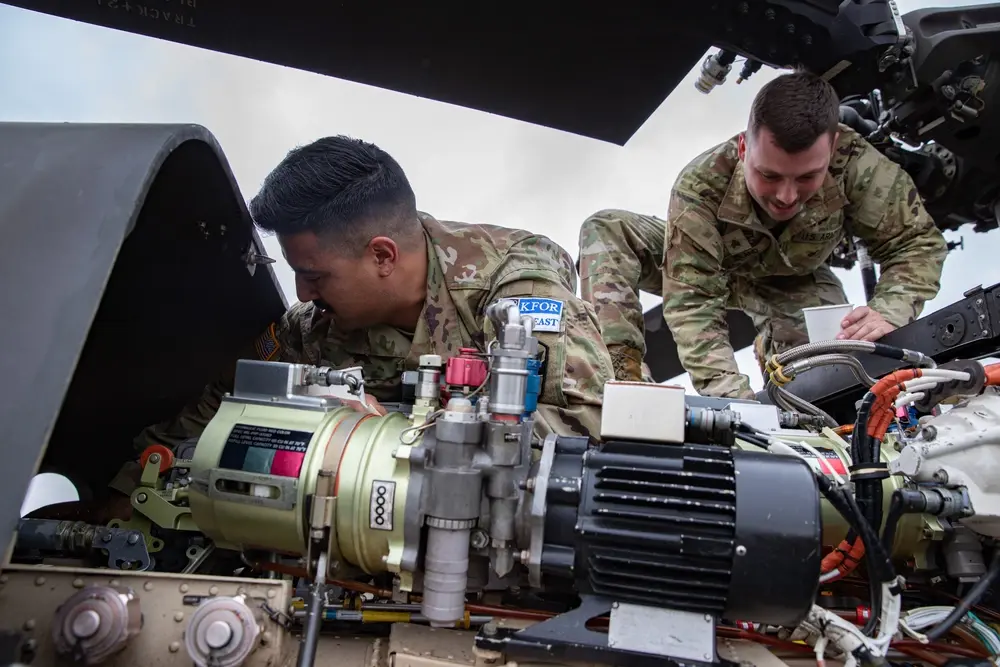
CAMP BONDSTEEL, KOSOVO
04.20.2023
Story by Staff Sgt. Anna Pongo
KFOR Regional Command East
CAMP BONDSTEEL, Kosovo – From carrying water to people who have none, to rescuing people in medical emergencies, Kosovo Force Regional Command-East’s (KFOR RC-E) Task Force Aviation works ceaselessly to ensure that the Soldiers and community in Kosovo are safe and secure.
Although, those who fly the helicopters couldn’t do their job without the mechanics who work long hours to keep the aircraft airborne. For these Soldiers with the 1-131st Aviation Regiment, Task Force Yellowhammer, from the Alabama Army National Guard, the behind-the-scenes maintenance they execute to keep the UH-60 Black Hawks flying, ensures the success of KFOR’s mission in Kosovo.
“For every hour of flight there is roughly 4 hours of maintenance that goes along with it,” explained 1st Sgt. David Forbes, the 1st Sgt. for D Co., 1-131st Aviation Regiment. “The flying part would not happen without the maintenance piece to keep them operating safely.”
All this responsibility means that often these Soldiers are working long hours.
“You will often find us out here until 8 o’clock at night on Saturdays, when most have already called it quits at noon,” said Forbes. “And then, depending on the mission requirements, we will most likely be out here on Sundays as well. There’s always something going on. There is not a lot of slow time in maintenance.”
The maintenance company is made up of 36 Soldiers who fall into the Headquarters Platoon, Component Repair Platoon and Allied Shops Platoon. Each works together to make the mission a success.
The Headquarters Platoon is made up of the command team, Production and Quality Control and Supply.
The members of Quality Control (TI’s) are the subject matter experts of aircraft. They look over each aspect of the repairs to ensure they are up to specifications and maintainers are capable of performing their job to standard.
“The most important part, you can’t fly without supply,” said Forbes. “We keep some bench stock here, but if it’s something big like a blade or an engine, it is ordered. – They are critical. Once we run out of nuts and bolts, someone has to be there to replenish that stock location.”
Spc. Courtney Martin, an Automated Logistics Specialist with D Co. expresses how the mission requirements affect her day-to-day job working in supply.
“My normal day is non-stop,” said Martin. “You’re either making sure that something is on order, placing an order for the guys or handing them parts that they need so the aircraft can keep running… This is the heart of aviation because your supply people have to keep everything ordered to keep everyone flying.”
The Maintenance and Component Repair Platoon is made up of the overall maintainers of the aircraft. The Soldiers’ military occupational specialties are Army UH-60 (Blackhawk) Helicopter Repairer, CH-47 (Chinook) Helicopter Repairer and AH-64 (Apache) Helicopter Repairer, but on this mobilization each works together to maintain the three medical specific UH-60Ls (Blackhawk) helicopters and six traditional lift UH-60Ls (Blackhawk) helicopters.
For these repairers, their daily tasks include removing and installing aircraft subsystem assemblies such as engines, rotors, gearboxes, transmissions and mechanical flight controls.
Finally, there is the Back Shops Platoon. “There you have engine shop-which is Power Plant,” explained Forbes. “You have Powertrain shop-which is drivetrain and transmissions, Sheet Metal shop-which is everything that has a screw go through it and blade repairs, and you’ve got Avionics and Electrical shop that kind of go (work) together.”
Each of these sections plays a vital role in keeping the helicopters safe for their missions.
Those who work in Sheet Metal have the additional challenge of being able to create composite work with fiberglass and sheet metal.
“We need to be able to think outside the box,” said Staff Sgt. Michael Hollingsworth, who is the non-commissioned officer in charge of sheet metal, one of the back shops section sergeants. “For a lot of our stuff, there is no right or wrong way of doing it because our job is so unique. It’s not cut and dry. We always have the challenge of trying to make something work, over just pulling and replacing a part.”
Being able to solve problems you may have not encountered before is a vital part of everyone’s job who works in D Co.
Staff Sgt. Shena Senatore works in Avionics and is a technical inspector for the unit AVNX/ELE and NVG shop. This means she looks at the repairs after they are complete to ensure that the aircraft is airworthy.
“It’s exciting to see them learn and troubleshoot and accomplish a task on their own,” said Senatore. “That’s one of my favorite parts of the job. It’s been a growing experience for all of us for sure, but luckily we’ve tackled almost all the preexisting faults. We’ve gotten our heads above the water and learned from them all.”
Though the primary goal for the unit is to keep the UH-60s flying safely every day, a secondary one is for each Soldier to gain new experiences and expertise in aircraft maintenance.
“We are always working to grow the maintainers and their skills,” said Forbes. “Cross training is important.”
Aircraft Pneudraulics repairer, Spc. Micheal Weaver is an example of this cross training. Through this deployment, he has learned many new skills to help in all areas of aircraft maintenance.
“I’ve been helping the 15Ts (UH-60 Blackhawk Repairers) with their inspections and the maintenance,” explained Weaver. “I try to get in with them and they teach me stuff so I can help out as much as possible. It’s been great training all around and if they need to operate the crane to pull an engine, I do that.”
Through all their hard work the Soldiers of D Co. have been able to ensure the success of aviation in KFOR and allowed them to log almost 1,500 hours of flight time across Kosovo.
“Aviation maintenance is the cornerstone of any aviation program,” said Forbes. “They go fly, but when they come back, they can’t go again until we do our thing.”