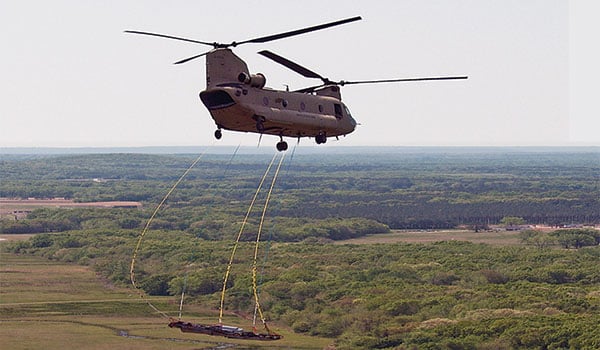
Aviation Support / By Amanda Medley: The personnel within the AGSE Product Office are dedicated to fielding, modernizing, and sustaining the Right Tools, at the Right Time, in the Right Place, ensuring our Soldiers have the most effective systems to conduct aviation maintenance any-where at any time.
AGSE recently completed a refresh of our “big three” Theater Provided Equipment (TPE) systems pre-positioned in Afghanistan: Standard Aircraft Towing Systems (SATS), Generic Aircraft Nitrogen Generators (GANG), and Auxiliary Ground Power Units (AGPU). Utilizing TPE for combat rotations rather than unit organic equipment unburdens units from packing and shipping these critical systems, significantly reduces inter- and intra-theater transportation costs, and reduces loss/damage from multi-modal transportation. An added benefit is preserving unit organic equipment and more importantly, time, for home station training. The strategy also extends operational use of the equipment, reducing Reset cycle times and saving Reset dollars. The TPE program has proven highly successful, saving the Army over $23M combined in transportation and Reset expenses. As Army Aviation enters future operations, AGSE will again look to employ a TPE system to support rotational deployed forces.

Modernized Unit Maintenance Aerial Recovery Kit (M-UMARK)
The Common Aviation Tool System (CATS) is rapidly fielding Army wide. As of 31 July 2015 we’ve fielded 12,218 CATS toolboxes to 46 Active Duty and National Guard units – over 50% of the Army requirement. We are well ahead of the initial fielding schedule and on path to have CATS fully fielded by mid-summer 2016. The CATS program has also fielded 13 toolboxes to one allied nation through Foreign Military Sales. CATS, a modernization of the New Aviation Tool System fielded in the mid-1990s, is an assortment of seven tool kits: hydraulic, powertrain, sheet metal, technical inspection, general mechanic, electrical, and power plant. All tools are designed to the latest aerospace industry standards and housed in foam shadowed drawers. Those units already fielded CATS know that six of the seven tool kits are fielded with an empty drawer. During the course of defining the original requirement, market research determined the required ratcheting wrenches were not Berry Amendment compliant. This information drove AGSE to strike them from the product item description but leave an empty drawer to facilitate adding compliant tools when they became available. Several major tool suppliers now offer a line of Aerospace Standard ratcheting wrenches assembled in the U.S., allowing AGSE to proceed with a Modification Work Order (MWO) to fill the empty drawers.
Fielding of these additional tools will begin in FY 2016.
Earlier this year, the Army approved a Capability Production Document for the Self-propelled Crane Aircraft Maintenance and Positioning (SCAMP) Increment II, and the Army Acquisition Executive delegated Milestone Decision Authority to PEO Aviation for the program. The system is comprised of two variants. First up for procurement and fielding is the expeditionary variant, optimized for air mobility in support of operations in austere environments on unimproved terrain. A flight line variant, optimized for efficiency in operations on improved surfaces and able to lift and reach the most extreme loads will follow. The expeditionary variant is scheduled to begin low rate initial production (LRIP) in 3Q FY17 and the flight line variant is scheduled to begin LRIP in 3Q FY20.

Aviation Light Utility Mobile Maintenance Cart (ALUMMC)
1st ACB, 4th CAB, and 10th CAB are participating in a Special User Evaluation (SUE) of the new Aviation Light Utility Mobile Maintenance Cart (ALUMMC), with 49 LRIP units being issued to each unit. Feedback has been tremendously positive and vignettes from home station training and combat training center (CTC) rotations continue to show the ALUMMC being employed in innovative ways, displaying the unbounded ingenuity of the Army Aviation Soldier! We anticipate Full Material Release in conjunction with a Full Rate Production Decision in February 2016.
Besides our new systems, modernization of our legacy systems is an important priority and we have many efforts initiated. The Modernized Maintenance Stand (MMS) will be an upgrade to the legacy B1 and B4 maintenance stands. Technical evaluation is underway of proposals received in response to this competitive commercial solicitation. After product verification testing and source selection is completed, we anticipate contract award and production to begin in the summer of 2016.
The Modernized Unit Maintenance Aerial Recovery Kit (M-UMARK) will provide units the ability to recover not only disabled rotary wing aircraft, but also crash/battle damaged rotary wing and Unmanned Aircraft Systems, including the MQ-1C Gray Eagle. The product team and AGSE Technical Division partnered with the University of Alabama in Huntsville (UAH) to design the M-UMARK and develop crash damage recovery procedures. Contract Award is on path for summer 2016 production.
Also slated for modernization are the A92 AVUM Shop Sets and Non-Destructive Test Equipment (NTDE) suites. The Modernized A92 has completed Critical Design Review and moved into Developmental Testing. The primary purpose of this upgrade is to replace the existing S-280 shelters with S-784/G 20 foot, one side expandable ISO compliant shelters for enhanced workspace and storage. The goal of the NDTE modernization is to replace now obsolete equipment.
Army Restructuring Initiative
PM AGSE is also playing a key role in the Army Restructuring Initiative (ARI) currently underway. While congressional committees continue to examine the remaining divestitures of OH-58D Kiowa and redistribution of AH-64 Apache helicopters through the Active Army and National Guard, AGSE is actively teaming with the Aviation Enterprise to analyze, plan, and support the many changes necessary to reach the Army’s desired force structure. Since ARI changes impact every AGSE program, it is critical we maintain open lines of communication with our stakeholders to assist in the management and movement of our equipment throughout the numerous Modified Table of Organization & Equipment (MTOE), Table of Distribution and Allowances (TDA), and Basis of Issue (BOI) changes and lateral transfers.
We know how critical your AGSE is to ensuring you meet your missions. When you need maintenance or additional AGSE information, your first stop should be the Joint Technical Data Integration (JTDI) site, https://www.jtdi.mil; select the AGSE tab for a variety of data. If you’re unable to find what you need, send us a help ticket by clicking on the AGSE Help Ticket. The AGSE Help Ticket System, https://agse.peoavn.army.mil/, is a second method of contacting support personnel you need. All tickets received via this system are actioned within 1 business day; users are provided updates on progress for issues that take longer than 1 business day to resolve.
Amanda Medley is a program integrator with the Product Management Office, AGSE, located at Redstone Arsenal, AL.