
Tech Talk / By Mr. David B. Cripps: The December 2015 edition of Army Aviation magazine featured a Tech Talk article on additive manufacturing (AM) that provided a brief description of various AM processes and gave a prediction that it would be several years before you saw 3D printed parts on an Army helicopter.
Like any new technology coming of age, there has been a lot of advancement in the last year, so an update is probably in order.
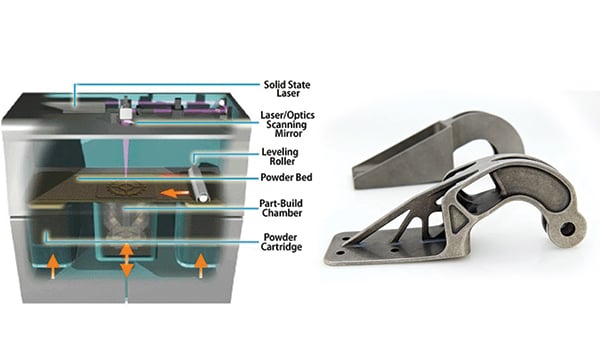
Direct Metal Laser Sintering Process (DMLS) left, and 3D Printed Airbus Part
For years there have been 3D printed parts flying on commercial airlines, but they have almost exclusively been in “non-critical applications,” such as the stowable arm that holds your in-seat video monitor. But there has been positive movement into more critical applications. One of the world’s largest manufacturers of turbofan engines for commercial jets has qualified fuel nozzles manufactured by means of direct metal laser sintering (DMLS), where a high power laser effectively welds powdered metal layer after layer, building up a part from a digital file. The company actually began work long ago in hopes of significant reductions in manufacturing cost, and the path to qualification was very long and arduous. The number of manufacturing variables for a process like DMLS is many times more than for more conventional manufacturing processes, and establishing the proper controls to yield a consistent product remains a very challenging task. The actual qualification effort is no more or less rigorous than for conventional manufacturing techniques. As with most fabrication processes, completion of the item to a finished product nearly always requires additional treatments and processes, such as surface finishing, heat treat, etc. The number of applications where you can take a part hot off the 3D printer and install them directly onto an aircraft will always be very few.
Just a few months ago, the U.S. Naval Air Systems Command flew two 3D printed titanium flight critical structural components in the nacelle of an MV-22B. The demonstration program is limited to 50 flight hours and has hundreds of strain gages applied to the two components and adjacent structure in order to investigate how closely the 3D printed parts match the performance of the conventionally machined parts they may eventually replace. While it is a limited demonstration, it is a huge step in the right direction.
Within the Army, there are also a few demonstration programs in the works, initially focused on components where the structural and vibratory loads are well understood and within the “comfort zone” of understanding of the performance of 3D printed metals. We are specifically looking at a gearbox housing and a particle separator swirl housing this year. More complex and heavily loaded components will follow.
Industry, academia and the Government are all working individually and collectively to mature the technology to a point where it not only offers an alternative to manufacturing components with existing designs but even beyond to where we can significantly alter our design approach to take more full advantage of the complexity that 3D printing can enable.
The logistics community is presently establishing requirements for a deployable capability to “print on demand” at the point of need, eliminating the requirement for transporting and pre-positioning vast amounts of spare parts. For today, that’s still Star Wars stuff. But every day it’s getting a little bit closer.
May the Force be with you!
Mr. David B. Cripps is the deputy director of the Aviation Engineering Directorate of the U.S. Army Aviation and Missile Research, Development, and Engineering Center at Redstone Arsenal, AL.